Жизнь заставила государство вплотную заняться отечественным производством. Наконец-то! Нам светит национальная технологическая инициатива «Новые производственные...», разработка которой уже началась силами институтов развития и научно-технического общества России. Хорошо бы в пылу погони за новыми производственными технологиями не забыть о классических и традиционных, которые, собственно, и обеспечивают нашу промышленность необходимым сырьем и материалами.
Но при ближайшем рассмотрении новое зачастую оказывается хорошо забытым старым. 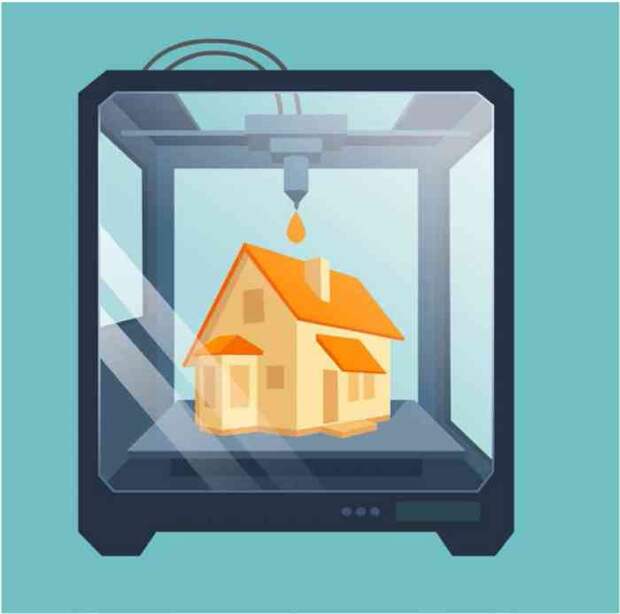
Аддитивные технологии: что это?
Человечество любит сходить с ума, был бы повод. Но мода всегда его находит. И тон тут задают не только дизайнеры. Вот и нобелевский лауреат Роалд Хофман считает, что миром правит мода. По его мнению, химию переименовали в нанотехнологии, чтобы увлечь молодежь новым модным словом, дать ей понять, что она работает в авангарде науки, на прорывном направлении.
Конечно, название очень важно само по себе. В нем должны быть интрига, некий парадокс и, конечно, английское звучание. Ну кто бы стал сходить с ума по стереолитографии? Громоздко, непонятно, слишком специально, а для специалистов — старо. Другое дело — 3D-принтинг, в считанные годы овладевший умами людей, даже далеких от технологического мира. Ведь принтер есть во всех офисах и во многих домах. И как же с его помощью напечатать не документ на бумаге, а объемную фигурку? Загадка. Хотя 3D-принтинг и стереолитография, по сути, одно и то же.
Но технологии развиваются. Не то чтобы вглубь — здесь наши желания упираются в границы применимости методов, но вширь — это точно. Множество вариаций этих методов, их различные применения теперь собраны под одной крышей с названием «Аддитивное производство», или «Аддитивные технологии».
С интригой в словах здесь не очень получилось, но звучит тем не менее вполне весомо, даже с претензией. Так на что же претендуют аддитивное производство (additive manufacturing) и его технологии? Суть аддитивного производства — в сложении, а не вычитании, в таком способе создания детали сложной формы, когда материал наносится последовательно, как правило, слой за слоем, поэтому расходуется его столько, сколько необходимо, не больше и не меньше. Процессом управляет компьютер, в чьей памяти заложена трехмерная модель будущей детали, нарезанная на тонкие слои-сечения. Устройство, подающее материал, скажем экструдер, движется по траекториям, заданным компьютером, слой за слоем конструируя будущее изделие. В общем — очередной виток автоматизации производства. Предполагается, что готовая деталь не нуждается в традиционной механической обработке. Так что аддитивное производство — это еще один способ изготовления деталей и предметов из разных материалов наряду с литьем, прокатом, штамповкой и резкой.
Аддитивное производство — понятие очень широкое, которое охватывает и многие классические технологии. Среди них создание полупроводниковых гетероструктур методами молекулярно-лучевой эпитаксии и CVD — химического осаждения из газовой фазы (1960-е годы), офсетная печать (ведет свою историю с XVIII века), нанесение многослойных покрытий на изделия разными способами, возведение кирпичной стены — «камень на камень, кирпич на кирпич», даже украшение торта кремовыми розочками, которые кулинар выдавливает из кулька или специального шприца, да и сам многослойный торт тоже. Гигантская скульптура «Рабочий и колхозница» В.И.Мухиной и Б.М.Иофана (1937) — пример аддитивного производства. Метровую модель скульптуры разрезали на слои, тщательно их измерили, затем размеры пропорционально увеличили и по ним изготовили деревянные формы, по которым, в свою очередь, выгнули стальные листы для каждого слоя, а их уже сварили в готовую скульптуру. Но сейчас мы говорим о новейших аддитивных технологиях, где главная роль отведена компьютерному моделированию трехмерных деталей любой сложности и их воссозданию слой за слоем с помощью автоматических систем.
Ничто не возникает на пустом месте, у всего в науке и технологиях есть предшественники. И хотя на протяжении последних 20 лет аддитивные технологии рассматриваются как нечто новое, их история насчитывает 150 лет, уходя корнями в такие области, как картография и фотоскульптура. Именно в этих областях деятельности впервые придумали разделить исходную модель на слои или фрагменты, а затем с их помощью воссоздать цельный объемный объект. В 1860 году французский скульптор Франсуа Виллем впервые сделал фотоскульптуру. Он оборудовал специальную круглую комнату, в которой был обозначен точный геометрический центр. В этот центр ставили или сажали в кресло человека, чью скульптуру предстояло сделать, и его одновременно фотографировали 24 камеры, встроенные в стены на равной высоте и равном расстоянии друг от друга. Так скульптор получал исчерпывающую информацию о модели со всех сторон и мог воссоздать ее в материале. Руками, конечно. В 1890 году Йозеф Блантер придумал послойный метод изготовления пресс-форм для печати рельефных топографических карт, на которых видны возвышенности, низменности и горы в строгом соответствии с топографическими линиями.
У истоков современного аддитивного производства стояла стереолитография. Она использовала подход, который придумал Отто Джон Мюнц в 1951 году. В установке Мюнца поршень в цилиндре смещался на маленькое расстояние и освобождал пространство для слоя, которое заполняли светочувствительным полимером. Затем полимер облучали светом так, что он застывал только на определенном участке. Следующее движение поршня — еще один слой, еще один цикл отверждения... В результате из многих слоев получалась объемная полимерная модель.
Это был ключевой принцип, который лег в основу современной стереолитографии (SL). Дальнейшие усовершенствования касались технических деталей — методов сканирования модели, способов формирования слоев из разных материалов, проецирования изображения и технологий отверждения (ультрафиолет, лазерный луч, электронный пучок и т. п.). В 1984 году Чарльз Халл запатентовал технологию и основал компанию 3D Systems, которая в 1986 году начала промышленное использование стереолитографии.
После изобретения принципа и его первого успешного практического использования события всегда развиваются по нарастающей. В 1985 году появляется технология ламинирования LOM (Laminated Object Manufacturing), в 1986 году — технология послойного наплавления FDM (Fused Deposition Modeling). Уже в 1990-х аддитивные технологии с использованием нагрева лазерным и электронным лучом для получения металлических объектов стали частью мирового производственного ландшафта.
Поначалу технологии создания трехмерных объектов называли «быстрым прототипированием». Название никакое. Но тут постарались студенты Массачусетского технологического института и в 1995 году предложили броский короткий термин «3D-Printing». Название понравилось, прижилось, стало модным. Хотя даже из этого названия следует, что 3D-печать лишь часть большой группы технологий, используемых в аддитивном производстве.
Завышенные ожидания
Всплеск в развитии аддитивных технологий пришелся на 2009 год. По мнению Королевской инженерной академии Великобритании, он связан с окончанием срока действия одного из ключевых патентов, который описывал метод FDM с использованием плавкой пластиковой нити. В результате цены на системы 3D-печати снизились в несколько раз, а инвесторы и производители немедленно обнаружили множество достоинств в аддитивных технологиях применительно к авиационной и автомобильной промышленности, к архитектуре и строительству.
Достоинства и преимущества, конечно, есть. Сам принцип сложения, а не вычитания подразумевает, что мы экономим исходные материалы. Не надо, подобно скульпторам, брать глыбу мрамора и отсекать все лишнее. Суть аддитивных технологий — использовать ровно столько материала, сколько требуется для создания объекта. Экономия материала в каждом конкретном случае будет различной, от небольшой до значительной. Если, например, у какой-то детали сплошные элементы заменить на ажурные без потери прочности (вспомним башни Шухова), то выигрыш будет очень большим. Ажурные детали сложно формовать штамповкой и литьем. А вот аддитивные технологии с этим справляются легко. И тогда создание шарнирного уголка гондолы для самолета, по оценкам European Aeronautic Defense and Space Company (Бристоль, Великобритания) и EOS Innovation Center (Уорвик, Великобритания), сэкономит до 75% исходного материала. Не говоря уже о том, что облегченные детали без потери прочности очень уместны в самолетах.
Вообще, аддитивные технологии теоретически позволяют изготавливать детали любой произвольной формы и любой сложности, например — изделия с внутренними каналами охлаждения. На токарном станке сделать это, мягко говоря, затруднительно. И конечно же трехмерные компьютерные модели деталей можно мгновенно передавать с помощью Интернета в любую точку мира — туда, где они требуются в данную минуту, на любое локальное производство. Поэтому стоимость и сроки запуска в производство какой-нибудь важной штуки заметно сократятся. Немаловажно и то, что детали можно делать только под заказ, штучно, и не накапливать их на складе. Так что плюсы, безусловно, есть.
Любая новая технология, прежде чем она займет свое место на рынке, проходит вполне стандартный путь «созревания», на котором, впрочем, может и умереть, не добравшись до финиша. Первые успешные попытки применения того или иного нового принципа на уровне прототипов порождают бум исследований и разработок и завышенные ожидания общества, достигающие пика. Затем разработчики, промышленники и общество «прозревают», осознают суровую реальность и начинают расставаться с иллюзиями. И только потом, скатившись с горы массового восторга, технология начинает медленно подниматься на плато, чтобы занять свое место на рынке. Точно такой путь проходят нанотехнологии. Они уже преодолели пик завышенных ожиданий в конце первого десятилетия XXI века, скатились в долину разочарования и теперь потихоньку, методично и без лишнего треска начинают взбираться на плато.
По оценкам компании Gartner, ожидания общества от технологии 3D-печати — соответствующий прибор в каждом доме, который позволит «печатать» самим все, что душе угодно, и не ходить в магазин, - сейчас находятся на пике. Это значит, что в ближайшие несколько лет она начнет скатываться с этой самой горы и лишь через 5—10 лет определит свое реальное место на рынке.
Пока что присутствие аддитивных технологий на мировом рынке более чем скромное — 2,2 млрд. долларов в 2012 году. Причем лишь 54% этой суммы приходилось собственно на продукцию технологий (26% — на производство оборудования , 19% — на производство исходных материалов). Но, как и любая новая технологическая отрасль, она характеризуется очень высокими темпами развития: среднегодовые темпы прироста в 2010—2012 годах составили 27%. Тем не менее Wohlers Associates оценивают рынок аддитивных технологий к 2021 году в размере всего лишь 10,8 млрд. долларов. Для сравнения: рынок продукции нанотехнологий в 2013 году превысил один триллион долларов (по данным Национальной нанотехнологической инициативы США).
Трезвый взгляд Сколтеха
Конечно, аддитивные технологии не универсальны. И конечно же любая технология имеет недостатки, ограничивающие и сдерживающие ее применение. В таблице представлен перечень технологий для аддитивного производства и материалы, которые они используют.
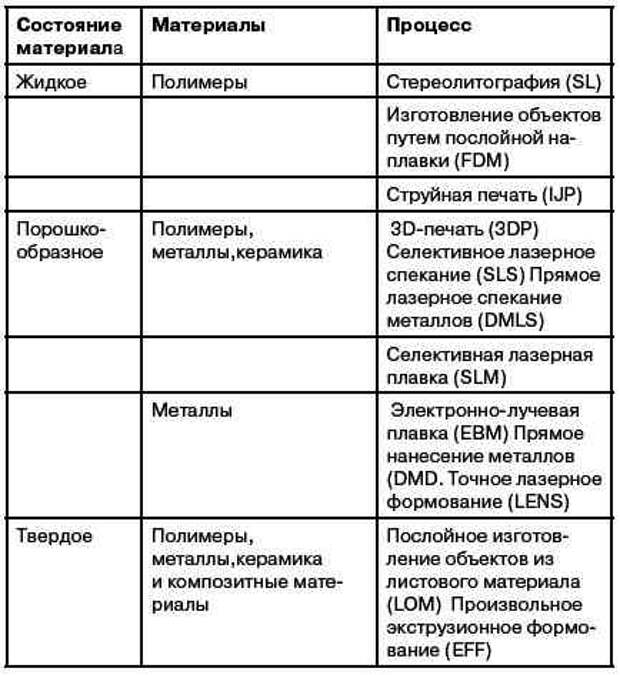
Материалы и технологии аддитивного производства Давайте посмотрим, где здесь таятся подводные камни.
Стереолитография — один из самых старых и заслуженных процессов, дающий наибольшую точность в изготовлении объекта и позволяющий контролировать его параметры. Схема процесса хорошо отлажена. Сначала создают компьютерную модель объекта, затем нарезают модель в STL-формате, чтобы получить набор сечений. Этот набор передают в стереолитографический аппарат, который управляет процессом послойного формирования детали в ванне со специальным полимером. Аргоновый лазер очерчивает двумерные сечения и заставляет полимер затвердевать. Если степень полимеризации недостаточна, то готовые детали помещают в УФ-печи, чтобы уж затвердело наверняка.
Стереолитографию сегодня применяют для быстрого прототипирования, когда нужно изготовить пробный образец чего-либо, для изготовления пресс-форм и форм для литья. Но есть проблемы. В ванне после процесса всегда остается неизрасходованный материал, который, впрочем, функционален — он поддерживает изготавливаемую деталь «на весу». Но его придется отделять, а это время и лишний расход материала. Кроме того, сами изделия из полимера, полученные таким способом, не отличаются долговременной стабильностью, поэтому технологию не используют для серийного производства деталей.
Метод послойной наплавки (FDM) тоже хорош для быстрого прототипирования. Из сопла-дозатора, движениями которого управляет компьютер, расплавленный материал (чаще всего — полилактид или акрилонитрилбутадиенстирол, то есть АВС-пластик) наносится последовательными слоями и быстро затвердевает, поскольку исходно он был нагрет всего лишь на градус выше, чем его температура плавления. При такой технологии точность изготовления детали не может быть высокой (не меньше 0,05 мм), она ограничивается размером сопла и другими факторами. Качество поверхности сильно уступает тому, что получается при литье. И, что очень важно, механическая прочность изделий оставляет желать лучшего. Дело не только в остаточных термических напряжениях, которые вызывают последующую деформацию, но и в ярко выраженной анизотропии, когда механические свойства детали разные по разным направлениям внутри материала.
Струйная печать (IJP, Inkjet Printing) наносит светоотверждаемые полимерные слои (как правило, на основе акрила) при помощи печатающих головок с множеством сопел. Поэтому скорость печати довольно высока. К тому же полимер отверждается ультрафиолетовым излучением непосредственно при печати. Технология дает относительно высокую точность и хорошее разрешение. Все вроде хорошо. Но изделия по своим характеристикам все равно проигрывают тем, что получены традиционным литьем. Они хрупкие! С материалами для этой технологии тоже проблема — выбора практически нет. Так что ее область применения ограничивается прототипированием и точным литьем единичных изделий.
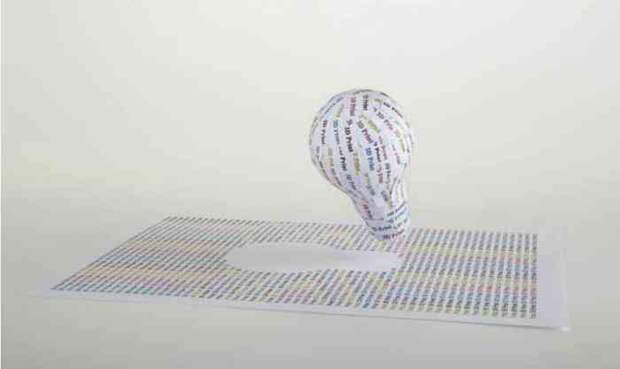
У технологий лазерного спекания (SLS, DMLS) свои трудности, хотя суть та же самая. Создается трехмерная компьютерная модель и нарезается на тонкие сечения. Специальный валик наносит на подложку слой (100 мкм) порошка (полимер, керамика, металл). Лазерный луч (мощность 25—100 Вт, длительность импульса 0,5—25 мс) очерчивает контур и спекает эту часть слоя. Затем валик наносит следующий слой порошка, и все повторяется. В чем проблемы? Проблемы в том, что в этих условиях трудно рассчитывать на полное плавление всех частиц порошка в слое, особенно если это легированный порошок. В результате получается неоднородная микроструктура материала, его механические свойства становятся хуже. Значит, деталь придется дополнительно нагревать, чтобы все там расплавилось. И зачем такая морока, если есть литье и прокат?
Так, может, сделать слой потоньше, а лазер помощнее, чтобы все уж заведомо расплавилось и спеклось? Именно так и поступают при селективном лазерном спекании (SLM, Selective Laser Melting), когда работают с порошками цветных металлов — титана, алюминия и меди: толщина порошкового слоя 20—40 мкм, мощность лазера до 1 кВт. Но чем тоньше слой, тем больше слоев, значит, время изготовления, и без того не маленькое, сильно увеличивается. А более мощный лазер, да еще с большим количеством слоев, съедает больше энергии. Однако, пожалуй, самое главное заключается в том, что при этой технологии детали склонны давать сильную усадку, вызывая значительные остаточные напряжения в изготовленных изделиях, которые, в свою очередь, могут вызвать деформацию и даже расслоение конечного продукта.
С электронно-лучевой плавкой - своя головная боль. Здесь круг используемых материалов ограничен проводящими электрический ток металлическими порошками. Сам процесс EBM выполняется в камере с глубоким вакуумом, что делает его довольно затратным, но, с другой стороны, облегчает работу с материалами, чувствительными к окислению.
Пожалуй, самый неоднозначный в этом ряду - это процесс послойного изготовления объектов из листового материала (LOM). Суть его в том, что изделие собирают из отдельных листов, вырезанных лазером, которые должны быть скреплены между собой. Здесь без ручной доводки, когда нужно убирать лишний материал и зачищать хвосты, не обойтись. Плюс ограниченная точность формирования изделий, неоднородность свойств материала, проблемы с долговечностью… На первый взгляд главная область его приложения — это прототипирование. Хотя у технологии, безусловно, есть потенциал, который еще предстоит раскрыть.
Подводя итог беглому экскурсу по основным аддитивным технологиям, следует признать, что количество факторов, сдерживающих распространение аддитивного производства, велико. Оборудование дорогое, материалы тоже, скорость изготовления маленькая, качество поверхности деталей таково, что необходима последующая механическая обработка, внутри детали наблюдается неоднородность свойств материала. Но главное, чего не приемлет серийное производство, — это плохая воспроизводимость, причем многоуровневая. На одной и той же установке получаются изделия с неодинаковыми характеристиками. Отличия усиливаются, если одну и ту же модель изготавливают на двух вроде бы одинаковых аппаратах одного производителя. А уж если взять оборудование от разных производителей и сделать на них модели по одному «чертежу», то различия будут еще более явными. Эта неустойчивость характеристик оборудования и продукции чрезвычайно затрудняет аттестацию и сертификацию, без которых никакое серийное производство сегодня немыслимо. Вообще, стандартизация новых технологий - глобальная проблема, которую сегодня решают уполномоченные государственные учреждения в содружестве с промышленными компаниями. Все это требует времени, усилий и ресурсов.
Однако перечисленные проблемы отнюдь не ставят крест на аддитивном производстве. Просто надо понимать, что у любой технологии есть границы применимости. А проблемы на то и проблемы, чтобы их решать.
Сегодня и завтра
Как-то пару лет назад представители современной модной молодежи, далекие, впрочем, от мира технологий, небрежно объясняли мне, что завтра никакие старые производства не понадобятся и все их закроют, потому что буквально всё будут печатать на 3D-принтерах. «И рельсы тоже будут печатать?» — спросила я. «И рельсы тоже», - получила я уверенный ответ. «А где будут брать материал для печати?» — решила я все-таки уточнить. «Да в магазинах купят!» — ответили мне собеседники совершенно серьезно.
Экономическая целесообразность и здравый смысл - вот что сдерживает распространение любых технологий. Зачем нам «аддитивные рельсы» и «аддитивные балки», если они дороже чугунного моста и в любой момент могут лопнуть? Зачем нам пластиковые бутылки и кружки, напечатанные на 3D-принтерах, если каждую надо печатать не меньше часа и стоит она соответственно гораздо больше тех, что производят серийно литьем и штамповкой?
Тем не менее у аддитивного производства со всей очевидностью есть ниша, которую можно описать так: производство единичных изделий и мелких партий уникальных деталей из дорогих материалов и в тех случаях, когда стоимость станочной обработки высока. На самом деле это очень большая ниша, начиная от ремонта и восстановления деталей сложных агрегатов и индивидуальных протезов до создания уникальных деталей сложной конфигурации.
Одна из сильных сторон аддитивного производства — штучное изготовление изделия любой формы. Как же это важно в медицине! И здесь аддитивное производство продвинулось довольно далеко. Сегодня методом стереолитографии успешно изготовлены и испытаны персональные сердечные клапаны, искусственные челюсти, части коленного сустава, акриловые краниопластические имплантаты (попросту — части черепа). Причем все эти детали сугубо индивидуальные, в точности повторяющие те, что приходится заменять. Два ведущих производителя слуховых аппаратов, Siemens и Phonak, применяют аддитивные технологии для изготовления индивидуальных устройств, точно соответствующих уху пациента. Компании могут сделать такие устройства за один день!
Так что медицина — обширное поле для аддитивного производства, начиная с изготовления специального хирургического инструмента, индивидуальных протезов, имплантатов и заканчивая тканями и органами из клеток человека.
Особый интерес к технологиям аддитивного производства проявляет авиационно-космическая промышленность. В общем-то оно и понятно. Эти отрасли требуют мелкосерийного производства высококачественных деталей, то есть штучного товара. Другое дело, что сертификационные требования здесь очень жесткие. Самолет — это не шутки, из-за поломки одной детали могут погибнуть люди. Да и на космическом корабле тоже. Тем не менее некоторые сертификаты уже выданы. Компания General Electric заявила, что готова к относительно массовому производству топливных форсунок для своего нового турбовинтового двигателя LEAP с помощью процесса DMLS из кобальтохромового порошка. Компания отметила, что может выпускать по меньшей мере 25 000 форсунок в год (одному двигателю требуется 19 форсунок).
Журналисты утверждают, что компания Boeing произвела методами аддитивных технологий более 20 000 деталей, которые уже используют в военных и гражданских самолетах компании. Множество SLS-деталей установлено на нескольких версиях военных самолетов, таких, как самолет дальнего воздушного радиолокационного обнаружения и управления, модели C-40, AWACS и P-8.
Аддитивные технологии оказались чрезвычайно востребованными для ремонта и восстановления деталей больших механизмов, скажем - турбинных лопаток. Расчеты показывают, что если в авиационном двигателе AV8B, сделанном из сплава титана, алюминия и ванадия, восстанавливать лопатки по технологии LENS, то можно сэкономить 715 000 долларов в год. Вообще, в литературе на эту тему много примеров.
Скажем, авиакомпания может сэкономить 2,5 млн. долларов только за счет того, что уменьшит на 50—80% вес металлических креплений в салоне. Именно это и позволяют сделать аддитивные технологии.
Компания Daimler AG (Штутгарт, Германия) в партнерстве с Concept Laser и Фраунгоферовским институтом лазерных технологий перешла на изготовление крупных функциональных металлических частей с помощью аддитивных технологий. Они позволили оптимизировать геометрию деталей и добиться снижения веса. Компания Local Motors с помощью 3D-печати изготовила первый пригодный для поездок автомобиль под названием Strati. Этот двухместный электрокар официально представили публике в сентябре 2014 года в Чикаго. Strati состоит всего из 49 деталей, включая напечатанный на 3D-принтере корпус, в то время как типичный промышленный автомобиль имеет в своем составе несколько тысяч деталей. Печать автомобиля из термопластика, усиленного углеродными волокна- ми, с помощью лазерной системы заняла примерно 44 часа. Автомобиль способен разгоняться до скорости 40 миль в час и проезжать на одной зарядке до 120 миль. Продажи Strati могут начаться в 2016 году, а его цена составит 18 000—34 000 долларов. Другим пригодным для эксплуатации электромобилем, изготовленным с помощью 3D-печати, станет Urbee 2, который будут делать с помощью технологии FDM.
Но пожалуй, самая просторная ниша для аддитивного производства — это товары широкого потребления. Компания FOC (Нидерланды) моделирует предметы обстановки (абажуры, стулья и другие декоративные элементы) и производит их из нейлонового порошка с помощью технологии LS по мере получения заказов через Интернет.
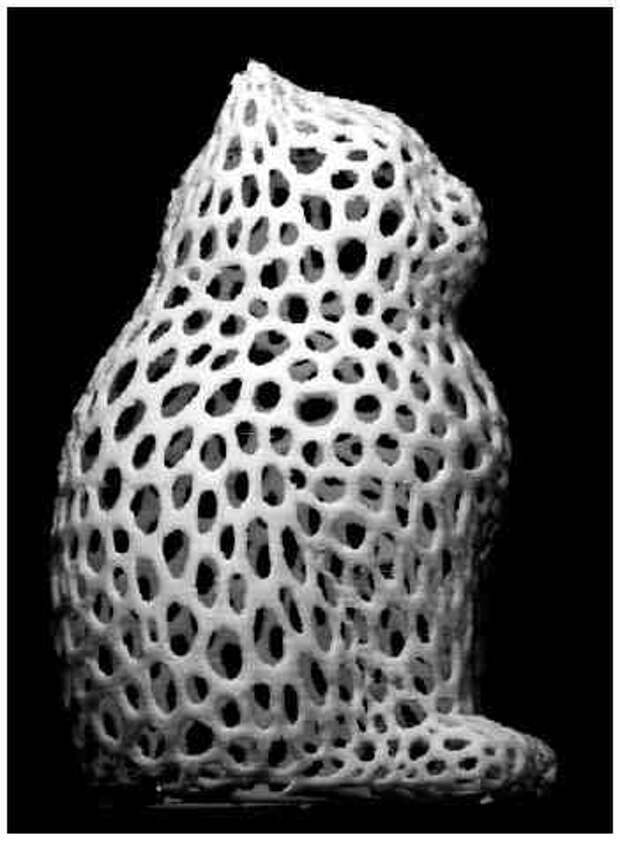
Ажурная фигурка кота. Когда речь идет об арт-объектах, 3D-печати нет равных.
Аддитивное производство дает больше свободы дизайнеру. В сущности — твори, что хочешь, все возможно. Поэтому неудивительно, что на подиум уже выходят модели в одежде из тканей, вышедших из 3D-печати, и в замысловатой пластиковой обуви того же происхождения.
Свобода проектирования распространяется и на клиентов, которые могут через Интернет самостоятельно управлять дизайном продукта. Компания Figureprints предлагает клиентам создать собственного персонажа игры World of Warcraft с помощью программы на сайте и отправить свой заказ производителю. Фигурку персонажа изготавливают на централизованном производстве и высылают заказчику. В игровой индустрии уже существуют сотни миллионов виртуальных персонажей, которых покупатели вполне могут захотеть превратить в физические объекты. По этой причине игровая индустрия может стать одной из самых привлекательных рыночных ниш для аддитивного производства.
Что же касается архитектуры и прикладного искусства, то здесь аддитивные технологии утвердились, видимо, навсегда. А как иначе создавать макеты новых зданий, сооружений и городов. Да и скульптуру проще «отпечатать» по модели (можно ведь и тиражировать), чем лепить руками или отливать из бронзы, — дорого!
В мире и в России
Аддитивное производство требует оборудования. Сегодня рынок соответствующих установок делится на три сегмента. Быстрее всего растет сегмент дешевых 3D-принтеров для офисов, ориентированных на изготовление концептуальных макетов. Второй сегмент - оборудование средней стоимости для создания прототипов деталей с различной степенью точности и/или функциональности. Дешевые и средние по стоимости установки обычно работают с полимерным материалом. Третий сегмент — установки высокого класса, которые стоят от двухсот тысяч до двух миллионов долларов. Они работают с полимерами, металлическими и керамическими порошками, с их помощью можно делать вполне крупно- габаритные детали. Ведущие изготовители установок — американские компании 3D Systems и ExOne, израильская Stratasys, шведская Arcam, а также немецкие EOS и Voxejet.
К 2013 году производством и продажей установок занимались шестнадцать компаний в Европе, семь — в Китае, пять — в США и две — в Японии. По числу смонтированных систем с большим отрывом лидируют США, собравшие у себя 38% промышленных установок. Значительное количество установок эксплуатируется также в Японии (9,7%), Германии (9,4%) и Китае (8,7%).
Доля России составляет 1,4%, что и понятно — научный задел России в этой области весьма невелик, всего 0,76% от мирового объема научных публикаций в этой области. За последние 15 лет в России был выдан 131 патент по различным аспектам аддитивного производства (0,14% от мирового количества), причем 14 из них получили российские заявители, а 117 — иностранные. Для сравнения: Южная Корея, США, Япония и Китай совместно владеют 90% патентов в этой сфере.
Что касается производства, то в России используют и внедряют аддитивные технологии считанное количество промышленных компаний и исследовательских центров в Москве, Санкт-Петербурге, Воронеже, Самаре, Ставрополе и Казани. Правда, в основном они продают западное оборудование и в лучшем случае занимаются прототипированием. Опять мы оказались в отстающих. Конечно, все объяснимо: оборудование дорогое, кадры надо готовить, производство соответствующих исходных материалов налаживать, стимулировать фундаментальные исследования и НИОКР.
Стрельникова Л.
Свежие комментарии